More about Windsor Chairs
Comfort first
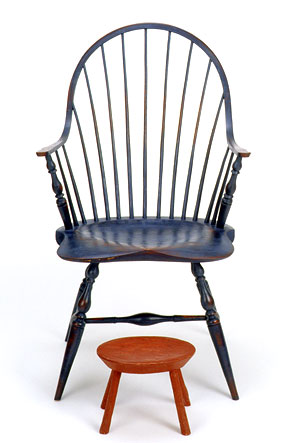
A Continous Arm Chair with Stool
My Windsor chairs are as comfortable as a dining chair can be. The seat is deeply scooped out to fit the anatomy and the flexible back is angled to support a comfortably upright posture for dining. I have attended to ergonomic details such as chair arms that are high enough to be restful while the sitter can maintain a straight spine. For those who desire an even softer seat, a tidy, thin cushion can be fashioned with tie strings to secure it to the posts.
Windsor furniture has great beauty
It is graceful, yet quaint. Elegant turnings, a boldly carved seat and gracefully arching bows pierced by a fan of slender spindles create a spacious silhouette. The chair captures the eye, yet allows the viewer to see through it to other features of the room.
Windsor chairs are strong and lightweight
Many 200 year old examples are to this day sturdy and tight, the result of a brilliant application of wood technology. Species of native wood are assembled by tools and techniques that were used in the eighteenth century. Straight-grained hardwood such as oak, hickory or ash is split and shaved along the grain to make a delicate spindle that is much stronger than it might appear. White oak is strong and readily steam bent to form the bow. Pine carves well for the seat, and hard maple makes beautiful turnings.
The construction of Windsor furniture:
The choice of wood
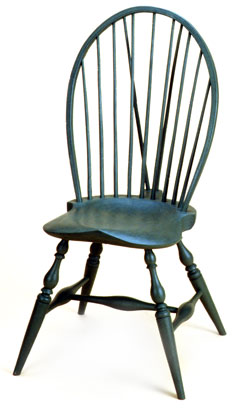
A Side Chair with Back Braces
Traditional wood species are used. Oak is steam-bent for the back bows because it bends well and remains strong and flexible. Spindles are of oak, ash, or hickory. The sugar maple used for the turned legs is very hard, thus it makes beautiful turnings that withstand generations of hard use. The seat is pine, and is usually of a single piece. It’s light weight allows for broad and deep dimensions for maximum comfort without making the chair cumbersome.
Lathe-turned legs and rungs are made of “green” or unseasoned wood. These parts are selectively dried so that after assembly, dry, pre-shrunken tenon ends are gripped by the shrinkage of the middle portions of these parts. This ensures joints that are guaranteed not to loosen.
The stock for all of the parts except the seat plank is “riven”, that is, split-out along the grain requiring that all crooked wood be rejected. This allows the chairs to appear to be delicate, but in fact they are very strong.
Traditional hand tools
Surfaces are generated by hand tools, not by power equipment and sandpaper. Tool marks are discreet, but are visible upon close inspection.
A beautiful absense of hardware
The tapered leg tenons are glued and wedged into tapered holes in the seat, forming a joint that will remain tight after many years of shrinking and swelling that occur with seasonal moisture changes.
In defense of paint
Milk paint makes a beautiful, authentic finish. It is not at all the thick coat which helped give paint a bad reputation in modern times. A uniform color enhances the striking silhouette of the Windsor style, and will not hide the tool marks characteristic of Windsor surfaces. Linseed oil over the paint brings up a discreet sheen and protects the wood. The paint wears in nicely, but will not chip, as it actually permeates the wood.
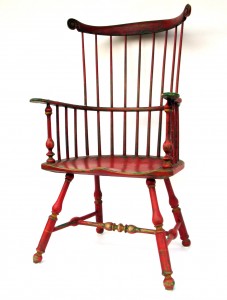
A well worn Comb Back Arm Chair
My most popular finish is milk paint. It is very thin, so does not hide the wooden character of the surface. The top coats (often black, green or blue) are rubbed through at areas of natural wear to reveal a different undercolor (often red). A crackled, antique finish, or a natural finish, are also available.
Chair design
The “continuous arm” Windsor is my favorite. It is most graceful, yet it is the strongest because the bow of the back and arms is of one continuous piece. This style is also the most comfortable as there is no rail across the back as in some other
chairs.